In today's interior customization industry, people's living standards are constantly improving, and the quality requirements for home life are becoming higher and higher. Correspondingly, the production level of various woodworking home products also needs to be upgraded accordingly. It is inevitable that the edge sealing of panel furniture is an important process in the furniture production process. Using adhesive to stick the edge sealing strip to the edge of the board is beautiful, moisture-proof, and non-volatile. So far, the biggest problem encountered in the edge sealing process is related to hot melt adhesive, which has a long heating time, increases energy consumption, and reduces edge sealing efficiency; Pollute workpieces and edge sealing devices, increase cleaning workload; Special heating and storage devices for hot melt adhesive are required. In addition, from the perspective of product aesthetics, the biggest drawback is the edge gap between the edge banding and the board. The longer the time, the more obvious the gap becomes, which affects the bonding performance.
Chengnuo Machinery takes this as the direction of improvement, and in 2022, it will devote itself to diligent research and development of laser technology, launching a new type of rectangular spot laser edge sealing technology (Laster Tec), pushing edge sealing technology to a new height. There is no need to clean the glue furnace or replace the glue, just replace the edge sealing tape according to demand, achieving true adhesive free edge sealing and injecting new industrial strength into the industry!
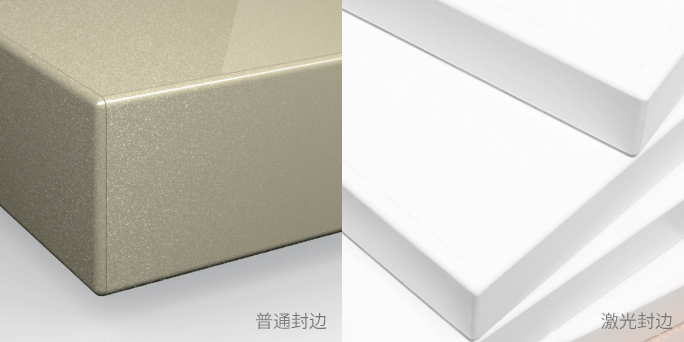
The principle of laser edge banding is that the edge banding has a two-layer structure, with the surface layer being a regular edge banding band and the bottom layer being a special functional polymer. Simply put, laser edge sealing technology uses laser melting of functional polymers to bond the edge banding with the sheet material, achieving strong adhesive strength and achieving seamless edge sealing. The entire process of laser energy concentration activates (melts) the functional layer with laser absorber, and the reaction time is rapid. Subsequently, the functional layer disappears. The entire process and materials are very environmentally friendly, without causing material loss or requiring additional secondary operations. Overall, the process of laser edge banding is basically the same as traditional edge banding, but laser edge banding simplifies the edge banding process due to the integrated production of edge banding tape and adhesive layer. Compared with traditional edge banding, it removes most unstable factors, reduces labor and energy consumption costs, is more automated, has more stable product quality, and is more aesthetically pleasing.
The laser emitter releases a high-energy rectangular laser spot, instantly melting the functional layer of the laser edge banding. The laser edge banding is tightly attached to the workpiece through the edge banding machine pressing wheel, and undergoes processes such as trimming, contouring, scraping, and polishing to achieve the ultimate seamless edge banding effect.
The advantage of rectangular spot is that the laser head uses optical transformation to quickly heat and melt the edge banding along the processing direction and combine it with the sheet metal to achieve a rectangular spot of the same height as the edge banding. Adjustable rectangular uniform spot<26m/min processing speed. The laser unit is equipped with a cooling system:
The system is equipped with a new type of diode cooling device, which can cool the laser when it occurs and remain in a waiting state at other times. Save energy consumption and greatly extend service life.
Advantages of laser edge banding machine:
- Separate cooling and output devices, with low requirements for coolant quality and low maintenance costs;
- Seamless edge sealing, zero glue line, more perfect appearance;
- No need for additional adhesive system configuration;
- No longer struggling with which glue to use;
- No need to wait, power on and edge sealing;
- No need for devices such as glue separation agents and cleaning agents;
Two different adhesive systems (laser+PUR) can be installed and activated according to requirements:
- Efficient processing, with a maximum speed of 26m/min;
- Equipment configuration includes track pressing, dual guide rail alignment, four blade profiling tracking, complete configuration, and strong functionality;
- The photoelectric conversion efficiency is over 30%, and the designed service life is up to 100000 hours;
- Accurate control of processing temperature, equipped with explosion-proof dust extraction system and cleaning processing to ensure safe production;
- No special environmental requirements, no need to worry about equipping a constant temperature and humidity factory environment;
- Improve product quality;
- Simplify the operational process;
- Reduce the cost of other auxiliary devices;
- Enhance the core competitiveness of enterprises;